在卧螺沉降离心机试中获得信心
要证明用于泥浆脱水的卧螺沉降离心机的性能,没有什么比试验技术更重要了。
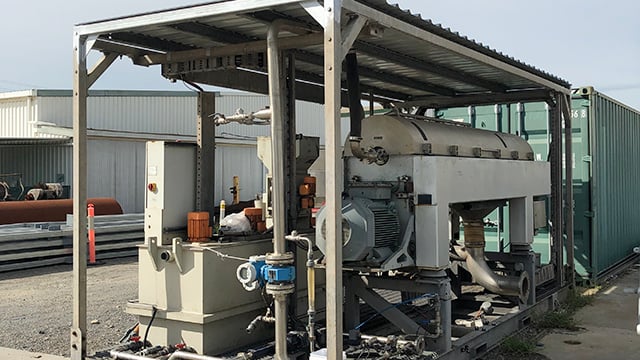
Alfa Laval portable skid mounted trial scalable decanter (solid bowl) mining centrifuge on a mine site.
Cake and centrate suitability
Along with proving the performance, the cake from a centrifuge can be stockpiled and used for downstream testing. This may include testing the transportability of the cake, or how well it tips out from a truck. It is not possible to do this from a spreadsheet study, and you may find that the transportable moisture limits are higher or lower than you expected.
Slurry mineralogy can vary significantly between different sites. For example, 35% moisture in a cake from one tailings source may be firm with a high shear strength. 35% moisture from a tailings source with a different mineralogy may be a sloppy cake. Holding some cake in your hands is a very effective way of analysing what the moisture level means for your unique situation. The results can be further analysed in a laboratory to quantify the rheology and transportability.
Additive optimisation
Many fine slurries require the addition of flocculent (and possibly coagulant) to achieve the required separation performance. The shear forces inside a centrifuge and feed slurry properties are quite different compared to dosing in a thickener, so specific decanter centrifuge work is needed for accurate flocculent testing. In a trial, there is an opportunity to optimise parameters by testing different additives, feed slurry densities, dosing points and additive concentrations. Determining the minimum additive cost with confidence cannot be achieved in a desktop study, but is an important financial and technical consideration in any decision.
Operator confidence
Plant operators and managers may be a little worried about someone changing the plant they are familiar with operating, particularly if they have not used the technology before.
A site trial is a great opportunity for operations personnel to see the technology in action and operate the centrifuge if they choose to. Being part of a trial on a production site will help to answer questions around maintenance, lubrication, start-up/ shutdown and reliability.
Capacity and Scale-up
If a trial is performed with a decanter centrifuge that is above scalable minimum size, the capacity and results can be scaled up. This is useful for obtaining the confidence for contractual guarantees for everyone involved.
Alfa Laval trial decanter (solid bowl) centrifuges for mining
Alfa Laval has a number of decanter (solid bowl) centrifuges available for trials on minerals processing slurries and tailings duties.
The smallest of these are pilot units with <40 kg/hr dry solids capacity, which is useful for conceptual testing and when only a small amount of feed slurry is available. The largest trial decanter (solid bowl) trial centrifuges can often handle > 50 dry tonnes per hour capacity. This gives the actual capacity, and therefore scale-up is not required. The most popular size for trials is one of our medium-sized machines, which can provide a scalable result with < 5 dry tonnes per hour feed capacity.
Alfa Laval maintains a fleet of these trial machines in Australia. The scalable and full-scale trial machines contain geometry and features specifically designed for inorganic mining slurries. Our local Australian field service and commissioning engineers are available for setting up the trial and training on operation. If your site happens to be in another country, Alfa Laval also has trial machines available in other global mining regions.
About the author
Paul Tuckwell Mining & Minerals Key Account Manager Alfa Laval Australia Paul is a Chemical Engineer with more than 22 years of experience in the fields of heat transfer, solid-liquid separation technologies and associated process engineering. He is based in Perth, Western Australia and is involved in minerals processing projects from conceptual stage to testing to final commissioning and beyond. Paul has a particular interest in sustainable tailings management and specialises in solid bowl centrifuges as a solution to dewater and stack solid cake instead of sending a slurry to a tailings dam. |